What Is Tqm In Business
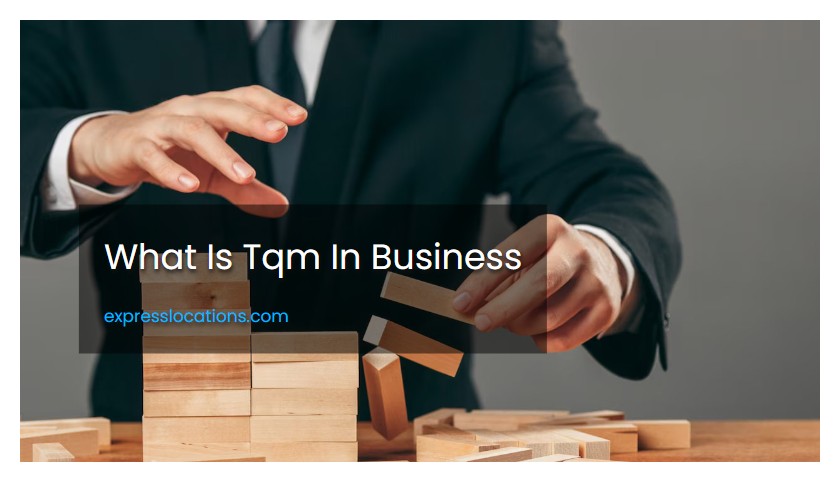
Total Quality Management (TQM) is a management approach that involves all members of an organization in the continuous process of detecting and reducing errors, improving customer experience, training employees, and streamlining supply chain management. TQM seeks to establish a culture of quality in a business to gain a competitive advantage and provide unparalleled customer satisfaction. It is a framework based on the belief that long-term success is achieved through focusing on improving quality at all levels of the organization. TQM is not a specific management tool or process but rather an approach that emphasizes quality and customer satisfaction to improve internal functioning.
Can you explain the basic principles of TQM in business?
Total Quality Management (TQM) implementation requires adherence to various principles, including continuous improvement, customer focus, strategic planning and leadership, competitive benchmarking, employee empowerment, teamwork approach, and knowledge of tools. These principles are common across all companies and are essential for achieving successful TQM. TQM is a long-term process aimed at improving a company's operations, with customer satisfaction being the ultimate measure of quality. Therefore, organizations that adopt TQM must focus on creating a customer-centric culture and empowering their employees to work together as a team to achieve continuous improvement. Additionally, leaders should be involved in setting strategic goals, benchmarking against competitors, and providing the necessary tools and resources to their teams.
What are the principles of TQM (Total Quality Management)?
In essence, Total Quality Management (TQM) is a set of principles aimed at improving the efficiency, effectiveness, and ultimately the satisfaction of both customers and employees. Among the key principles of TQM are a customer focus, involving employees in the process, taking a process-oriented approach, integrating systems, making decisions based on facts, and fostering communication. By implementing these principles, organizations can achieve greater success in meeting customer needs while also empowering and engaging their workforce.
When do TQM tools and principles acquire power?
In brief, Nichols posits that the effectiveness of Total Quality Management (TQM) tools and principles is harnessed not through the formation of a designated quality department, but by incorporating the entire organization into the pursuit of optimizing quality. He cites quality circles as an example where employees involved in a process collaborate to identify solutions.
How to implement process approach in TQM?
To effectively implement the process approach in Total Quality Management (TQM), it is imperative to utilize tools such as process flowcharts to delineate clear roles and responsibilities. This ensures that everyone within the organization comprehends their duties and the appropriate timelines for their execution. By doing so, it enables the team to work together cohesively towards achieving the goals of TQM. In essence, the process approach is a critical aspect of TQM, and utilizing it appropriately can assist in facilitating an improved organizational culture, streamlined processes, and ultimately, better outcomes.
What is the difference between traditional and Total Quality Management?
The difference between traditional and total quality management lies in their fundamental philosophy, implementation, and measurement. In traditional quality management, supervisors typically dictate what employees must do, based on the organization's short-term goals. Conversely, total quality management emphasizes the involvement of all employees in the continuous improvement of processes and products, to achieve long-term organizational success. Total quality management can be more complex and demanding to implement than traditional quality management, but it ultimately aims to create a culture of quality and excellence throughout the organization. Both approaches have their benefits, and businesses must choose the method that aligns best with their goals and values.
What is the difference between TQM and traditional set up?
In contrast to traditional business practices, Total Quality Management (TQM) prioritizes quality as the primary factor in a company's success. The consequences of poor quality include not only immediate financial losses but also negative impacts on a company's reputation, customer loyalty, and competitive advantage. In contrast, TQM facilitates ongoing improvements in all aspects of a company's operations through a commitment to continuous learning and development. The benefits of TQM include increased customer satisfaction and retention, cost reductions through efficient processes, and improved overall performance.
Which companies practice Total Quality Management (TQM)?
Toyota, the biggest auto manufacturer globally, is renowned for its successful implementation of Total Quality Management (TQM). The company's TQM approach centers around analyzing customer behavior and preferences, allowing for improvements to be made in its products. This has resulted in Toyota being a leading brand in the automobile industry, and serves as an example of how TQM can be adopted to enhance business operations in various industries.
What is TQM certification?
In summary, TQM certification is a professional training program intended to provide individuals with the knowledge and skills to implement Total Quality Management principles in their workplaces effectively. It is not a certification that is administered by any official body, and organizations cannot be certified as TQM. Instead, the program is usually offered by educational institutions as a means of ensuring that individuals are equipped with the necessary tools to improve product and service quality and overall business performance. By focusing on continuous improvement and customer satisfaction, TQM training can help organizations develop an effective quality management system.
What are some common tools and techniques used in TQM implementation?
Total Quality Management (TQM) is a business philosophy centered on preventing problems through continuous improvement of processes and products. In support of this philosophy, several TQM tools have emerged as essential aids for identifying and addressing potential issues before they occur. These tools include checklists, fishbone diagrams, histogram charts, Pareto diagrams, the PDCA cycle, process flow charts, and process control charts. Each of these tools serves a specific purpose in the TQM process, allowing businesses to stay ahead of problems and maintain a consistent level of quality across all aspects of their operations.
What TQM tools can management use in Total Quality Management?
Total Quality Management (TQM) is a management approach that emphasizes the participation of all employees in achieving superior quality in products and services. TQM tools are essential in achieving this goal, and one such tool is the Pareto Principle, which states that 80% of a problem arises from 20% of its causes. By identifying and addressing these primary causes, TQM can improve the overall quality of the product or service. Other TQM tools include benchmarking, process mapping, flowcharting, statistical process control, and customer feedback surveys. The use of these tools can help organizations to identify and eliminate the root causes of defects in their products or services, resulting in better quality and increased customer satisfaction.
How does top management decide to commit to TQM?
The adoption of Total Quality Management (TQM) as a strategy by top management is a critical step towards ensuring quality improvement in the organization. To kickstart the TQM initiative, the organization must first assess its current culture, customer satisfaction levels, and quality management systems. Once the assessment is complete, top management should establish core values and principles that will guide the implementation of TQM and communicate them to all stakeholders. By taking these steps, the organization can ensure that TQM becomes an integral part of its operations and that it delivers sustainable benefits to the organization and its customers.
Can you share some success stories of TQM implementation in businesses?
The implementation of total quality management (TQM) has led to notable success stories within various industries. Companies such as Xerox, Allen-Bradley, Motorola, Marriott, Harley-Davidson, Ford, and Hewlett-Packard have been able to achieve significant improvements in their operations and customer satisfaction through the adoption of TQM principles. This demonstrates that the systematic and continuous approach to enhancing product and service quality has a positive impact on business performance. The success stories of TQM provide compelling evidence of the benefits that can be achieved through a commitment to quality and continuous improvement.
Can a business benefit from TQM?
Total Quality Management (TQM) can greatly benefit businesses that lack a clear path to creating satisfied customers. While customer satisfaction is crucial, it is not the only factor in achieving success. In order to be successful, a business must satisfy customers in a cost-efficient way. TQM can help businesses achieve this by implementing quality processes and continuously improving upon them to ensure customer satisfaction and business success.
What are the success stories of Total Quality Management?
There is an article discusses the success stories of the implementation of total quality management (TQM) in various companies, including Xerox, Allen-Bradley, and Ford. The author highlights how TQM has challenged management theory and practice, emphasizing the need for continuous improvement and employee involvement. By guaranteeing customer satisfaction, TQM has become a valuable tool for companies in a highly competitive market. The author argues that TQM's success hinges on its ability to align management practices with the values and goals of the organization. Overall, the article presents TQM as a viable approach to achieving long-term success and improving business performance.
What companies are committed to TQM?
The implementation of Total Quality Management (TQM) has brought significant improvements to various companies such as Xerox, Allen-Bradley, and Marriott. These companies have embraced TQM by making substantial changes to their management practices and philosophies, resulting in better product quality and overall company performance. TQM has presented a challenge to management theory and practice by requiring a comprehensive approach to quality that involves the entire organization. As a result, companies that have successfully embraced TQM have reaped the benefits of sustained success and improved customer satisfaction.
What is a TQM problem?
Implementing a Quality Management System (QMS) poses several risks, including misplacing, changing, damaging, or losing critical internal documents. Additionally, companies may lack sufficient resources and manpower to execute a QMS that would facilitate a Total Quality Management (TQM) resource for automotive customers. Delays in implementation and completion of approvals and changes can also occur. Despite these challenges, many companies have successfully implemented QMS and have reaped the benefits of improved quality, increased customer satisfaction, and reduced costs. Case studies of such companies can provide useful insights into effective ways of implementing QMS.
What is the role of employee involvement in TQM implementation?
Total employee involvement is an essential component of an effective total quality management (TQM) implementation. It emphasizes the participation and engagement of each employee in the pursuit of continuous improvement and competitiveness. This approach encourages employees to learn and develop new skills, which can result in improved quality and customer satisfaction. The successful implementation of TQM requires a commitment from all employees towards a common goal, and total employee involvement enables this by empowering each team member to contribute to the organization's success.
How important is employee involvement in quality management?
Employee involvement is of utmost significance in ensuring the success of quality management plans. Employees play a vital role in maintaining the flow of operations similar to that of worker bees in a hive. However, their participation and commitment to strategies and objectives are crucial. The involvement of employees has been widely recognized as the cornerstone of quality management success. It is important to foster a culture of employee involvement to maintain and improve the effectiveness of the quality management plans.
What is the role of HR and quality policies in TQM?
Alignment of human resource and quality policies is crucial in preparing organizations and their employees for Total Quality Management (TQM) implementation. This includes creating and communicating a TQM vision, which generates quality awareness among employees at all levels and functions. This ultimately contributes to the improvement of employee performance. Research suggests that organizations that establish alignment between HR and quality policies have a greater chance of successfully implementing TQM and achieving their quality targets.
How does TQM impact customer satisfaction and retention?
Total Quality Management (TQM) plays a vital role in enhancing customer satisfaction levels by focusing on the development of high-quality goods and services. By prioritizing quality in business processes, companies can increase their value to customers and justify higher prices. This approach leads to improved customer loyalty and positive brand reputation, which are essential for long-term success in any industry. Therefore, TQM is a critical factor in building a sustainable business model that meets the needs and expectations of customers while increasing profitability.
What is total customer satisfaction (TQM)?
Total Quality Management (TQM) is a management approach that aims to achieve the ultimate goal of total customer satisfaction by managing all aspects of quality. All functional areas of the organization must adhere to the quality plan and strive to meet the planned quality targets. The key objective of TQM is to ensure that every task or product is of the highest possible quality. This approach requires a continuous effort to improve all processes and systems within the organization, and to involve all employees in the pursuit of excellence. Ultimately, TQM is about delivering consistent quality to customers and achieving a competitive advantage in the marketplace.
Does Total Quality Management affect customer satisfaction of automobile industry?
According to economists, the dissatisfaction of customers in the automobile industry can be attributed to the failure of Total Quality Management (TQM). In view of this, this study aimed to examine the effect of TQM on customer satisfaction, as a means of promoting sustainable development in companies in the automobile industry. The findings of this investigation can provide valuable insights for firms to enhance their TQM practices, and thereby improve customer satisfaction, which is crucial for long-term growth and success.
Does Total Quality Management affect patient satisfaction?
The study examined the impact of Total Quality Management (TQM) on patient satisfaction in the healthcare industry. The results showed that TQM had a significant effect on perceived service quality, which in turn, positively influenced patient satisfaction. The study presented a model demonstrating that both TQM and perceived service quality exerted direct influence on patient satisfaction. The findings highlighted the importance of implementing TQM practices to improve customer satisfaction in healthcare settings. The study's formal tone emphasized the rigor and validity of the research, enhancing the credibility of the results.
What are some potential challenges business face during the TQM implementation process?
In summary, the research has identified several challenges that organizations face when implementing quality initiatives. These challenges include a lack of creativity and innovation in decision-making, difficulties in managing a decentralized quality workforce, the failure to analyze or reengineer business processes, and the absence of a quality management committee. Addressing these obstacles is crucial in ensuring that quality initiatives are successful and contribute to the overall organizational performance. Therefore, it is essential for organizations to develop comprehensive strategies that prioritize innovation, effective communication, employee engagement, and collaboration to overcome these challenges and promote success.
What are the factors affecting the implementation of TQM?
According to a recent study, the successful implementation of Total Quality Management (TQM) is dependent on several factors, including management commitment, the role of the quality department, and training and education. However, challenges to implementing TQM include the lack of readily available quality system documentation, insufficient understanding of process requirements, and the high cost associated with implementation. These findings shed light on the obstacles that organizations must overcome when attempting to implement TQM successfully.
Are training programs necessary for implementing Total Quality Management (TQM)?
The effective implementation of total quality management (TQM) requires appropriate training programs for the workforce. In Kohat District, Pakistan, public secondary schools encounter significant challenges in implementing TQM. The current study investigates these challenges to identify the barriers to successful TQM implementation. Understanding these challenges can help public secondary schools in Kohat District and other organizations overcome any obstacles and reap the benefits of TQM.
What challenges Halt the purpose of quality management?
In implementing Total Quality Management (TQM), challenges may arise that hinder the purpose of quality management, such as constraints imposed by the lack of a genuine quality culture. This can result in resistance to change and reluctance to accept new techniques that can improve the current style of working. It is important for organizations to address these challenges in order to successfully implement TQM and achieve continuous improvement.
How difficult is it to implement a Quality Management System (QMS)?
The implementation and maintenance of a Quality Management System (QMS) can be a daunting task, given the multiple challenges faced by quality management professionals. Access to reliable information, an appropriate methodology, qualified personnel, and adequate time are not always readily available. Therefore, it is essential to identify the challenges that may arise during the implementation and maintenance phases of a QMS. By doing so, organizations can proactively address these issues, and ensure that their QMS delivers the expected results in terms of consistently meeting customer and regulatory requirements.
What are some critical success factors for TQM implementation in businesses?
To achieve successful Total Quality Management (TQM) implementation in a company, several essential factors must be considered. Firstly, there must be a strong commitment and understanding of TQM policies from top management down to every worker. Secondly, maintaining a focus on meeting customer requirements is crucial for effective TQM. Additionally, employee involvement and participation, regular training and education, clear communication, and fostering a culture that promotes continuous improvement are all vital components of TQM implementation. By addressing these core factors, a company can increase its chances of achieving sustainable TQM and improving overall organizational performance.
What are the key factors for a successful TQM implementation?
In order to achieve successful Total Quality Management (TQM) implementation, there are six essential factors that must be considered. Firstly, senior leaders must provide the initiative and support to implement quality programs. Secondly, customer focus is crucial for identifying and meeting customer needs. Thirdly, a systematic approach to management should be adopted to ensure consistent and effective processes. Fourthly, continuous improvement needs to be embedded into the company culture. Fifthly, employee involvement is important for encouraging ownership and commitment towards quality programs. Finally, training and education should be provided to ensure that employees have the necessary knowledge and skills to implement TQM successfully. By considering these factors, companies can improve their quality programs and ultimately enhance their overall performance.
What is the importance of teamwork in TQM?
The importance of teamwork in achieving organizational goals is highlighted by Rao, who also emphasizes the significance of including teams in any Total Quality Management (TQM) approach. Process management is considered one of the most widely used quality management principles in both manufacturing and service industries. The effective implementation of TQM can be influenced by various critical success factors.
What is the literature review on Total Quality Management critical success factors?
This systematic literature review analyzed total quality management (TQM) critical success factors and identified new avenues of research. The review examined relevant articles and found that leadership, employee involvement, customer focus, and continuous improvement were consistently identified as critical factors for TQM success. However, the review also revealed gaps in the existing literature, particularly regarding the integration of TQM with other management systems and the impact of cultural factors on TQM success. This study provides important insights for organizations seeking to implement TQM and highlights areas where further research is needed to fully understand and optimize TQM implementation.
Can Six Sigma and lean be used together with TQM?
There is an article explores the similarities and differences between three popular quality concepts: Total Quality Management (TQM), Six Sigma, and Lean. It highlights the benefits of each approach and provides guidance to organizations on their applicability and properties. The paper suggests that TQM, Six Sigma, and Lean can be used individually or combined to create a comprehensive quality management system. The authors emphasize the importance of understanding the unique features of each concept, and tailoring the approach to suit the organization's needs and goals. The article provides a valuable resource for managers seeking to improve their organization's quality performance.
What is the difference between Total Quality Management and lean manufacturing?
In brief, Total Quality Management (TQM) and Lean Manufacturing differ in their approach to managing quality in business operations. TQM provides general techniques for maintaining quality throughout an organization, whereas Lean Manufacturing focuses on optimizing production processes by reducing waste. The emphasis on efficiency in Lean Manufacturing can lead to improved quality as a secondary benefit resulting from streamlined workflows and procedures.
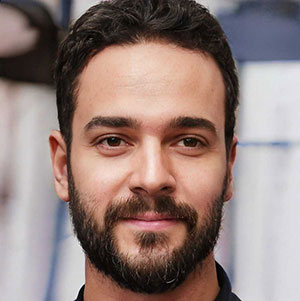